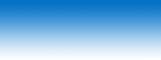
Copyright © 2009-2020
North Manchester
Historical Society
All rights reserved.
Please contact
our Center for History
if you find
inaccuracies or
inappropriate content.
|
Source: Aurora (1935) Ad:
THE HECKMAN BINDERY
906 N. Sycamore St. N. Manchester,
Ind.
OLD BOOKS MADE LIKE NEW
At Very Reasonable Prices
School and Library Books Bibles
Hymnals
Class Notes Term Papers
Steven Heckman - A History of the Heckman Bindery
Source: NMHS Newsletter May 1993.
Presented
July 12, 1992 to the North Manchester Historical Society
This is the first time anyone has asked me to do this,
so I had to do some digging which was fun.
Yesterday I got out the old reel-to-reel tape recorder.
I was married in 1971. In 1973 I asked my grandmother
Sanger (used to be Grandmother Heckman) to come over for
dinner two different nights. One night she talked an
hour about the origination of the Heckman Bindery. The
next time she came over she talked about my father and
grandfather-how they came to North Manchester. So it
took me about 2 1/2 hours to get the reel-to-reel
working yesterday. It was a rainy day so it didn't
matter. I listened to that for 2 hours and it was really
interesting. I appreciate the opportunity to do this.
What I plan to do is to give you a little bit about the
present but since you are a historical society I assume
that you are more interested in the past. So I'd like to
not dwell too much on the future and present, but I
would like to run an 11 minute video which is a working
plant tour for those of you who have not taken our plant
tour.
After the video...
Our employment is now 400 people and in the summertime
we employ an additional 75. Summer is a pretty busy time
around the Heckman Bindery.
I would like to distinguish between edition binding and
library binding. A lot of people think we are book
binders and we are. So is R. R. Donnelly. They are known
as edition binders. They are very equipment and capital
intensive and not very labor intensive whereas we are
the opposite. We are not very capital or equipment
intensive. We are mostly labor intensive.
The library binding business is one at a time. The
edition binding business is 50,000 of a title running
through this machine and falling out complete on the
other side. Every periodical that is bound must match
identically the previous bound volume. The spine must be
the same height, same lettering, same position of
lettering, same color of bucram. In other words, we are
binding to match and every single volume in the plant is
one of a kind. You see stacks and stacks of books
throughout the plant. Every single volume and every
single stack is different size, shape and title. So that
distinguishes us between library binding and edition
binding. Our little niche in the world is to serve
libraries. The reason that our binding is superior to an
edition bound book is not because they have shoddy
workmanship at R. R. Donnelly. The reason is that 10% of
books that are manufactured actually end up in the
library. They are usually passed around from individual
to individual and they do not need to be bound that
strong. That is our little niche in the world. It is
serving libraries.
It is a very demanding, complex business really. I have
a lot of people to manage because it is so labor
intensive. We are in the trucking business. We have to
pick up and deliver all this material. We more closely
resemble a commercial dry cleaner than we do a book
binder, in the sense that we have to pick up the
material no matter where it is in the U. S., bring it
back to North Manchester, render the service, return it.
A very, very small portion of our sales dollar is
actually raw material. It is mostly labor. So we have
pick-up, delivery service. We have a lot of people to
manage, and I must say, I would not want to be located
in any other place in the world than North Manchester,
Indiana. We have such a strong work ethic, and we have
such a good character of our people in this community. I
grew up here and I'm glad I did.
After I am through I will open up to questions. I will
make a deal with you: I will talk as long as you want me
to - as long as you feel free to walk out any old time.
You won't hurt my feelings at all. I know you all have
different interest levels and different pressures on
your time.
I brought some pictures from our archives. While I was
digging through these pictures this morning I found a
letter that my grandmother had written in 1957. This
letter was written to a Mrs. Howe, who apparently had
asked for some information as to how the bindery
started. This is dated October 1, 1957.
"Dear Mrs. Howe:
"You asked for some early history of Heckman Bindery. I
will tell you as best I can remember. It was the Spring
of 1931. The depression was on us. Paul (Steve's father)
and a friend planned a trip to California with the
intent of binding and repairing old books on the way to
help pay their expenses. Local college and high school
boys had been doing this sort of work in the area. Being
depression time, librarians were glad to have this kind
of repair work as they were short of funds. The trip to
California had to be a little delayed. So the boys asked
to work in our basement, which we let them do.
"Their equipment consisted of a small library table,
small hand press, scissors, table knife, needle and
thread, and a shoemaker's awl. They would go to schools
and libraries, pick up books and bring them to our
basement for repair. This was done by tearing off the
old book backs, punching holes with an awl through the
back edge of each book, sewing with a needle and thread
and putting the back on again. Not a very nice looking
book when finished.
"The boys would not be able to put in full time as they
were also working at other jobs. Vernon and I (Steve's
grandfather and step-grandmother, Mary) got interested
in their work, tried our hand at it and tried to make
improvements in methods. The boys finally gave up the
California trip and the binding business. Book binding
became a hobby with Vernon who was only working part
time at Peabody Seating Co. This gave him the
opportunity to get out and collect books from schools
and libraries.
"Paul did go to California for about six weeks. Letters
came from Paul to carry on and he would be back in the
spring to book bind again. He came back in March, 1932.
Meanwhile, we had moved from the basement to the kitchen
and the dining room. Vernon and Paul then remodeled the
garage into a place more suitable. Paul took over the
printing of book spines and traveling. This gave his dad
more time for rebinding.
"By this time we had a small printing press to take the
place of hand printing titles with a pen onto the spines
of books. We also obtained our first paper cutter which
was used for trimming old edges from books. With more
work and machinery to operate we hired our first help.
Winnie Baker Landis took my place at bookkeeping.
Charles Ruppel, Jr. was printer and on the trimmer. Fern
Miller did the sewing and back making. Also Mrs. Heeter
and Charles Bundy and Ralph Talmadge.
"Now we were so crowded again that the sewers and
bookkeeper were in our house working again. We worked
this way during 1933 and 1934. In the fall of 1934 Paul
took a notion to go to California again. He sold his
share of the bindery to me for $76. Vernon had quit his
job at Peabody's and was putting full time in traveling,
collecting, and delivering books. Before spring 1935,
Paul was ready to come back. I sold my share back to
him. He took over the traveling and selling. In 1936 we
were crowded again. The garage bindery was not large
enough to handle the volume of work. In the fall of that
year we built a small building in one corner of our
garden. Now we thought the crowded conditions were over.
We had some college students working part time and
bought more machines. We were in need of an office girl
so Mrs. Blanche Baker Wilcox came to our assistance
during her vacation from teaching. Grace McNear was our
next office girl. In the spring of 1938 it was necessary
to do something again about crowded conditions. Work had
grown so that part of it was back in our home again. The
finished work was carried there for sorting, billing and
shipping. The property north of our home was for sale.
We were fortunate to get that. The little garden bindery
was moved to the property and joined at the back of that
house. It wasn't long until another addition was added.
By 1940 we were crowded again. A two story cement block
building was joined at the back-about 70 ft. X 35
ft.-plenty of room we thought. More machinery was added,
power sewing machine, trimmer, backer, etc. This took up
considerable space so more was built across the back
yard of our home. This set-up was used until 1955 when
the building for the present bindery was started. The
new building was planned before Vernon's death on May
20, 1955 and work had started on it that day.
"Sincerely, Mary Heckman"
I listened to the tape recorder and picked up a few more
facts you might be interested in.
Vernon's first big order was 300 books from Chili
School, near Roann. The second big order was 900 books
from Albion schools. The typical pickups were a dozen or
2 dozen books. The one that was really responsible for
early success was when my dad got back from California,
and somehow Dr. Huff at Ft. Wayne Public Library found
out about Heckman Bindery and came over to look us over.
Apparently he liked what he saw. He said, "There's no
way you can do this work in this small space. If you'll
go ahead and build your space, we will give you enough
work you'll have no problem justifying that space."
That's what led to the garden bindery-the little
dwelling in the back yard.
The first employees earned 50¢ a day. Emery Baker built
the garden building-50¢ an hour in 1935. It cost $300
total, 24 ft. X 36 ft.
In 1936, they bought the house and property next door
for $1200. They moved the garden building over and
attached it-then added a 70 ft. long building. Next they
bought 3 acres next door. That was at the edge of town.
It was a field. That's where the present bindery sits.
Nineteen additions have been made to the present
building, which now totals 100,000 square feet.
On the rest of the tape my step-grandmother, Mary,
talked about Vernon and Paul and herself. Vernon was the
youngest of 13 children. He was born September, 1884,
near Dayton, Ohio. His parents were Samuel and Anna
Heckman. He married Izetta Eikenberry in 1906. They
moved to North Manchester. Izetta's father moved his
family to a farm near Sidney and Vernon and Izetta moved
with them. Vernon didn't like farm work particularly but
worked there awhile, then at Peabody's. He was with
Peabody's for 25 years, off and on. He was in shipping
and packing department-school seats. He and Izetta had
one son, Paul, my father. Izetta died in 1920. My dad
was nine years old. In 1925 Vernon married Mary Fulton.
Vernon died in May of 1955. Mary married Perry Sanger in
Sebring, Fla. He died in 1974 and she died in 1976. Paul
was born June, 1911. He died in 1973 as a result of an
automobile accident-that was my dad. He married Sarah
Studebaker from Tipp City, Ohio. She's still living, in
Sebring, and she oversees a motel our family owns down
there. She lives there full-time. She was back last
weekend for a family visit. She comes back about once a
quarter. She was a Studebaker. They had two children,
myself and 10 years later my sister Kay, who is a social
worker in Indianapolis. She's never been married, loves
her job in social work, working with blind people in
Indianapolis.
The home where the bindery began at 906 N. Sycamore is
still here. It is pretty much as it was in those days. I
did put aluminum siding on it and rent it out. Vernon
actually moved that house from the Sidney farm to that
location, after he built a basement. Vernon left for a
year during the time he worked for Peabody's to work for
Akron Rubber Company in Akron, Ohio. He ran out of work
when the war ended. He came back to work at Peabody's.
Paul went to Central High School, as did I and my sister
Kay. We had nearly all the same teachers-Dad and I
did-even my sister 10 years younger. Leigh Freed, Owen
Moore, Warner Ogden, Louise Dingle, Bagwell. I had five
or six teachers my dad had, and my sister three. Now
they've torn the school down so I have nothing to
remember. My dad was born in North Manchester. Some of
his jobs during high school: he sold pop corn to
Marshall Theater and Min Hite lived around the corner.
She would pop the corn, he would sell it and she would
walk him home at night so he didn't get in any trouble.
She lost her son in an automobile accident and kind of
took Paul under her wing. He worked behind the soda
counter at Burdge's Drug Store. He went to Manchester
College for one year, but I don't know what year that
was. He sold shoes and clothing at Grisso's Clothing
Store and then he sold menswear at Brady's Mens' Store.
I think he sold All-State Insurance while doing the
bindery thing. Then he sold that agency to Leslie Yoder
for $500.
Mary Sanger was the chief operator or manager of four
different telephone companies. She started at Laketon
where she grew up, then worked in Peru, Valparaiso, and
finally North Manchester. My grandfather met her while
she was working in Valparaiso. His first wife had died
five years previously and someone arranged their
meeting. Those are some facts that I thought might be of
interest to you.
The following section includes responses Steve gave to
questions asked by the audience.
Most of the work is library binding. We are a
$10,000,000 company with 400 employees. We are very
labor intensive. We have 90% devoted to library binding
for colleges, universities and public schools. There are
three other divisions which are smaller.
1. Conservation of rare and valuable books and
documents. We are the largest in the country to my
knowledge who are doing it commercially. There are some
private institutions who are doing it too. We have a lot
of capabilities. The only capability we don't have is
gold hand tooling. A dream of mine for a long time has
been to hire an artist, probably from Europe, to set up
shop in that Heckman home and maybe move our entire
conservation department over there. I would like to have
that skill. It would be an interesting thing for people
to see plus it would be a sales tool for us too. Other
than that we have all kinds of capability. We are able
to make different kinds of enclosures for books that are
too brittle to actually sew. We can make a container for
them that sits on a shelf like a book.
If you have anything rare and valuable we're the place
you should bring it. We have someone coming through our
front door every 15 minutes with this old family Bible
or pulpit Bible or whatever. The people back there are
wonderful. They have had a lot of years of experience
and they can make a shabby book look good again with the
original cover. Sometimes they have to put some leather
inserts in.
2. Super short run edition bind. That is, if a genealogy
group, for instance, wants to put together a genealogy
and they want only 100 or 500 copies, or even 25, we do
this kind of book. A college professor writes a book,
wants only 50 - 100 - 500 copies, we do that type of
thing. We have these two special departments separate
from each other and from our library division. These are
growing all the time-a lot of interest in that. The big
guys find it a real pain for them to deal with these
small quantities. I'm talking about 10,000 as a small
quantity.
3. Not Library Binding- Summer textbooks. In the summer
we do 150,000-200,000 text book repairs. They come with
"Tommy loves Suzy" all written on, all beat up, and we
put them in a binding that is actually better than the
original binding. It's a big economic savings for the
institution that has them bound. If taxpayers really
realized that, they would have everything rebound, I
think. The publishers add a few words and call it a new
edition and charge a whole bunch of money for a new
book. How many math books need to be changed that often?
This is basically a ten week season. We also have
Follett Book Company in Chicago that does textbook
rebinding with us all year long.
These are the three little divisions.
We used to serve everybody the same. We'd pick up one
box of books from "Podunk High School" or a few books
from some public library in the state of Ohio and would
treat them just like our very large college and
university accounts. About ten years ago we decided we
seemed to be better at binding periodicals than anything
else. Why not capitalize on what we do best. We started
really specializing in colleges and universities and we
are all over the United States. The Library of Congress
is one you hear about the most because they have been
our customer for so many years. Our largest state is
Texas. We send a truck down to Dallas once a month; two
weeks later we send one to Houston. It seems like a long
way to travel but the volume of work is so great, the
distribution costs are not that great. We have done the
University of Virginia for as long as I can remember. We
have a distribution center in Front Royal, Virginia.
We've had it for 45 years probably. That has something
to do with the Library of Congress because they are only
60 miles down the road from the Library of Congress. Our
45 foot trailer runs out there every weekend to drop off
a trailer full of newly bound books and picks up a
trailer just like it full of books to be bound. We have
a guaranteed schedule we have to meet. It's another one
of the difficult things. It doesn't matter whether it's
a "zillion" books which come in or just a few. We have
to get those books back to that library on the exact
date we promise. We work a lot of time during the summer
because people send their periodicals after the July
date and send them after the January date. We absolutely
starve to death in the fourth quarter. October, November
and December are pathetic. Everybody is upset-every
year. We try to tell them when we bring new employees in
that this is a fact of life at Heckman Bindery. We work
4 days, sometimes even 3 days a week during the fourth
quarter. The work just is not there. We've tried
everything but libraries are going to send the work when
they want to send it. If you work at Heckman Bindery you
are going to get some slow time-some time off during the
fourth quarter of the year.
Following are responses from Steve Heckman to questions
and comments.
Regarding size of the operation:
We are $10,000,000 in sales. We have a competitor now
who's been going out and buying binderies up in various
locations. He has five plants now and he is about the
same size we are-by putting all those plants together.
We are not totally the big guy now-one competitor. Then
it drops down to about half dozen in the United States
of $2,500,000. There are about 100 binderies in the U.S.
Most of them are very small. All of them are family
owned in the U.S. Our trade association has about 40
members. They control about 80%-closer to 90% of the
total sales in the U.S.
We bind anything that has pages. We bind newspapers,
hymnals, theses. A big product in recent years- 30
years- is paper backs. Obviously paper backs don't last
long in libraries, so we have two different methods.
1. Heckman paper back binding we've had for many years.
We bind it, then mount the paper covers on the outside.
2. Milar binding- we actually bind the covers so you can
see through it. The good thing about those are they are
very attractive and they catch the eyes of the children
and others. The bad thing is they are very slippery.
We do anything where you need pages put together.
Regarding trucks:
Out of Front Royal, Virginia, we have a half dozen. Out
of North Manchester we have about eight. As I said
earlier, we used to treat everybody the same. We used to
have a lot of trucks and a lot of branch offices. We
realized we could not handle those distribution costs
any more. They were eating us alive. At one time we had:
a distribution office in Sterling, Illinois; Huntsville,
Alabama; one man office in Tyler, Texas; one man office
in Ocala, Florida; the main office we've always had in
Front Royal, Virginia. We had to say, "Look, we like to
think we're on base. Give us a little more protection
but we just can't afford to pick up all that material
every week. We went for bigger customers and now we have
a little "sweat-out" like today we all sat around a
table. The Library of Congress is up again. A couple
weeks ago we all sat around the table- Texas was up
again. This is all contract work. There's some loyalty,
but mostly you have to have the low price. That means
you have to be very, very efficient.
Regarding restoration:
We have two methods: aqueous and non-aqueous. It all
depends on whether the inks may or may not run. We have
to establish that at the very beginning.
Aqueous process- we actually dip the separate pages in
water. We wash the pages in water, separate the pages,
then dry them, dip them in solution.
Non-aqueous- brush on chemical, or can also dip that in
the chemical solution.
The Library of Congress has helped us a lot in the
restoration department. Fifteen years ago they decided
they would also (we do all their library binding) give
us a shot at doing some of their rare books. We've
worked on their rare art book collection for about 15
years-50 volumes every week-sometimes 25. That's where
we learned our skills. We have always done family
Bibles. We got into the rare book thing in a big way. We
sent people out to the Library of Congress to train;
they'd send people to our place to help us, so they
basically trained us.
Regarding customer relations:
The customer's always right. We replace books if the
customer says we lost them. Even if we don't think we
did.
Regarding future growth:
I'll tell you what is happening. Our industry has not
necessarily been declining, but just stable for 15 or 20
years. We feel the money is better spent trying to
acquire some of our competitors than trying to come out
with the lowest prices. We bought a company in
Cincinnati, Ohio, about a year and a half ago. Very nice
acquisition. We have it almost paid off now. We've
increased our sales as a result. We are now looking at
about a half dozen different binderies to acquire. Our
preference of course is to bring them back to North
Manchester. That is probably how we'll grow in the
future-through acquisition.
Regarding Vernon and the house:
He was a pretty innovative guy. He also had a hobby of
fixing music boxes. Before we actually needed the space,
he had the whole upstairs of the old part of the bindery
which is still in existence. It is across the street
from our present bindery. It was filled with music
boxes, organs, player pianos-anything he could get his
hands on. He was good at that. He was a craftsman, loved
the idea of improving the craft.
My dad's strengths were in sales and he also loved the
material handling part. If you have been through our
plant, you've noticed we don't have any tables
whatsoever. We have roller conveyors, some of them are
on air cylinders-go up and down. I'd hate to be buying
that right now at today's cost. That was one of his
contributions. Another of his contributions was the
machine shop. We've made at least half of the equipment
in our plant. We are a small industry so the major
machine makers are not going to knock themselves out to
sell just a few machines. We have come up with our own
ideas, create our own. We have a wonderful machine shop.
Every time we have a problem, they create some kind of a
device to fix it.
Regarding Steve's interest in the business:
I went to Indiana University after I graduated from
Central High School. After four years I went to service
for two years. I took my last 30 day leave to come back
to get started in the bindery. I love the work. It gets
frustrating sometimes. My weekends are fun but I'd just
as soon go to work on Monday morning. I love the people
I work with. It is a good feeling we are doing something
noble, helping educate our future generations.
Conservation of the written word.
Regarding jogging:
Well, I get run over. I have a problem because I'm not
very temperate. I like to eat too much, so I do it for
exercise. I've been doing it since 1968-that four miles.
Only problem is my joints are giving out. I guess I'll
have to try something else.
*************************
Discussion of owning property at Winona Lake.
Grandparents and father Paul both owned cottages at
Winona. Lived here in winter and at lake in summer.
Steve chose to live at Winona Lake and commute.
Discussion of father's interest in horses. He owned 150
acre farm. At the time of Paul's death he owned 60
horses (registered quarter) and 150 black angus cattle.
Paul was the only one in the family who liked the farm.
Sally Allen shared a story of a horse Paul kept on the
property next to them. He kept a Tennessee Walking horse
on the lot behind the bindery.
Discussion closed with reference to students who work at
the bindery and also of those who have in the past.
Steve invited Historical Society members to visit the
bindery-we would be welcomed to plan such a visit, as
they enjoy showing people through their business.
|
|